while both Nickel 200 and Nickel 201 are pure nickel alloys, Nickel 201 has better resistance to reducing environments due to its lower carbon content. The choice between the two would depend on the specific application requirements and the environment in which the material will be used.
Nickel 200 and Nickel 201 are both commercial pure nickel alloys that differ slightly in their chemical composition.
Nickel 200 is a ferromagnetic, commercially pure (99.6%) nickel alloy with good mechanical properties and excellent resistance to many corrosive environments, including acids, alkalines, and neutral solutions. It has low electrical resistivity, making it suitable for electrical and electronic applications.
Nickel 201, on the other hand, is also a commercially pure (99.6%) nickel alloy but has lower carbon content compared to Nickel 200. This lower carbon content gives Nickel 201 better resistance to corrosion in reducing environments, such as sulfuric acid. It is also commonly used in chemical processing, electronic components, and rechargeable batteries.
In summary, while both Nickel 200 and Nickel 201 are pure nickel alloys, Nickel 201 has better resistance to reducing environments due to its lower carbon content. The choice between the two would depend on the specific application requirements and the environment in which the material will be used.
Nickel200 is a commercially pure wrought nickel alloy that consists of 99.6% nickel. It is known for its excellent corrosion resistance, high thermal and electrical conductivity, low gas content, and good mechanical properties. It can be easily fabricated and has low creep rates, making it suitable for a wide range of applications including chemical processing, electrical components, and marine environments. Nickel 200 is also non-magnetic and has a high melting point, making it useful in high-temperature applications.
Nickel201 is a high-purity form of nickel metal. It is a commercially pure alloy, meaning it contains 99.6% minimum nickel content, with very low levels of other elements. Nickel 201 is known for its excellent resistance to various corrosive environments, including acids, alkaline solutions, and seawater. It also exhibits good mechanical properties and high thermal and electrical conductivity.
Some typical applications of Nickel 201 include chemical processing equipment, caustic evaporators, hydrochloric acid production, pharmaceutical equipment, synthetic fiber production, and sodium sulfide production. It is also used in electrical and electronic industries for components requiring high electrical conductivity.
Overall, Nickel 201 is valued for its high purity, excellent corrosion resistance, and resistance to embrittlement at high temperatures. It is a reliable choice for various industries where these properties are required.
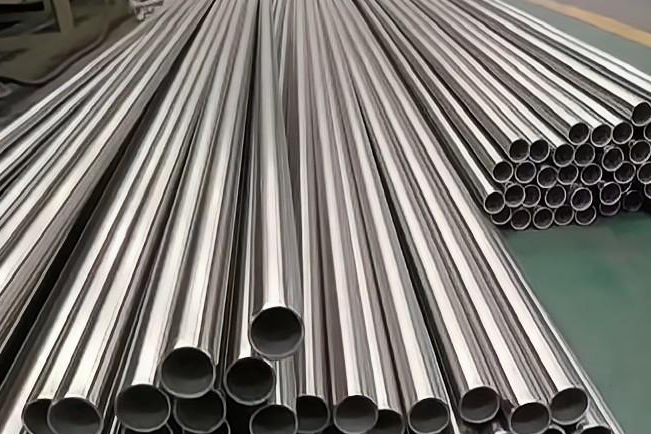
One of the key differences between Nickel 200 and Nickel 201 is the carbon content. Nickel 201 has a maximum carbon content of 0.02%, which is much lower than the maximum carbon content of 0.15% in Nickel 200. This reduced carbon content in Nickel 201 provides improved resistance to graphitization, a process that can lead to embrittlement and reduced strength and impact resistance of the alloy at high temperatures.
Due to its high purity and enhanced resistance to graphitization, Nickel 201 is commonly used in applications that require exposure to elevated temperatures and reducing atmospheres. It is often chosen over Nickel 200 for its ability to maintain its mechanical properties and resistance to embrittlement in such environments.
Nickel is a versatile and widely used metal due to its excellent properties, such as corrosion resistance, high temperature resistance, and electrical conductivity. One of the popular nickel alloys is Nickel 200, known for its purity and high corrosion resistance. However, there is another variation of this alloy called Nickel 201, which has a slightly different composition and properties. In this article, we will explore the differences between Nickel 200 and Nickel 201 and their respective applications.
Nickel 200 is a pure nickel alloy with a minimum nickel content of 99.0%. It is known for its exceptional resistance to various corrosive environments, including acids, alkaline solutions, and seawater. This makes it an ideal choice for applications where corrosion resistance is critical, such as chemical processing, food processing, and marine industries. Additionally, Nickel 200 exhibits excellent thermal and electrical conductivity, making it suitable for electrical and electronic components, as well as heat exchangers and high-temperature applications.
However, despite its excellent corrosion resistance, Nickel 200 is susceptible to embrittlement and reduced impact strength when exposed to temperatures above 600°C, especially in reducing environments containing sulfur or sulfur compounds. This is where Nickel 201 comes into play.
Nickel 201 is also a pure nickel alloy, with a slightly lower carbon content compared to Nickel 200. The maximum carbon content for Nickel 201 is 0.02%, while Nickel 200 has a maximum carbon content of 0.15%. This reduced carbon content in Nickel 201 provides improved resistance to graphitization, a process of forming carbon particles that can reduce the alloy's strength and toughness at high temperatures. As a result, Nickel 201 is often preferred over Nickel 200 in applications requiring exposure to elevated temperatures and reducing atmospheres.
The resistance to graphitization makes Nickel 201 highly suitable for applications involving caustic evaporators, hydrochloric acid production, and other chemical processing equipment. It also finds applications in the pulp and paper industry, as well as in the production of synthetic fiber and sodium sulfide. Additionally, Nickel 201 is non-magnetic and shares similar excellent properties as Nickel 200, such as high corrosion resistance, thermal conductivity, and electrical conductivity.
Choosing between Nickel 200 and Nickel 201 depends on the specific requirements of the application. If superior corrosion resistance is the primary concern and operating temperature does not exceed 600°C, Nickel 200 is an excellent choice. Its higher carbon content does not pose any issues in most applications, and it offers a cost-effective solution for many industries. However, if the application involves high temperatures or reducing atmospheres where graphitization may occur, Nickel 201 should be considered for its enhanced resistance to this phenomenon.
It is essential to consult with industry professionals, such as material engineers or metallurgists, to determine the most suitable nickel alloy for a specific application. They can consider factors such as the operating environment, temperature, and any potential concerns related to embrittlement or graphitization. With their expertise, they can guide users in making the right choice for optimal performance and longevity.
In conclusion, Nickel 200 and Nickel 201 are both excellent nickel alloys with slight differences in composition and properties. Nickel 200 offers exceptional corrosion resistance and electrical conductivity, while Nickel 201 provides improved resistance to graphitization at high temperatures and reducing atmospheres. Choosing the right alloy for a particular application depends on the operating conditions and desired properties, and expert advice is recommended to ensure optimal performance. Whether it is Nickel 200 or Nickel 201, these alloys continue to be widely used in various industries for their versatility and reliability.
Post time: Jul-18-2023